Electronic components Obsolescence Management
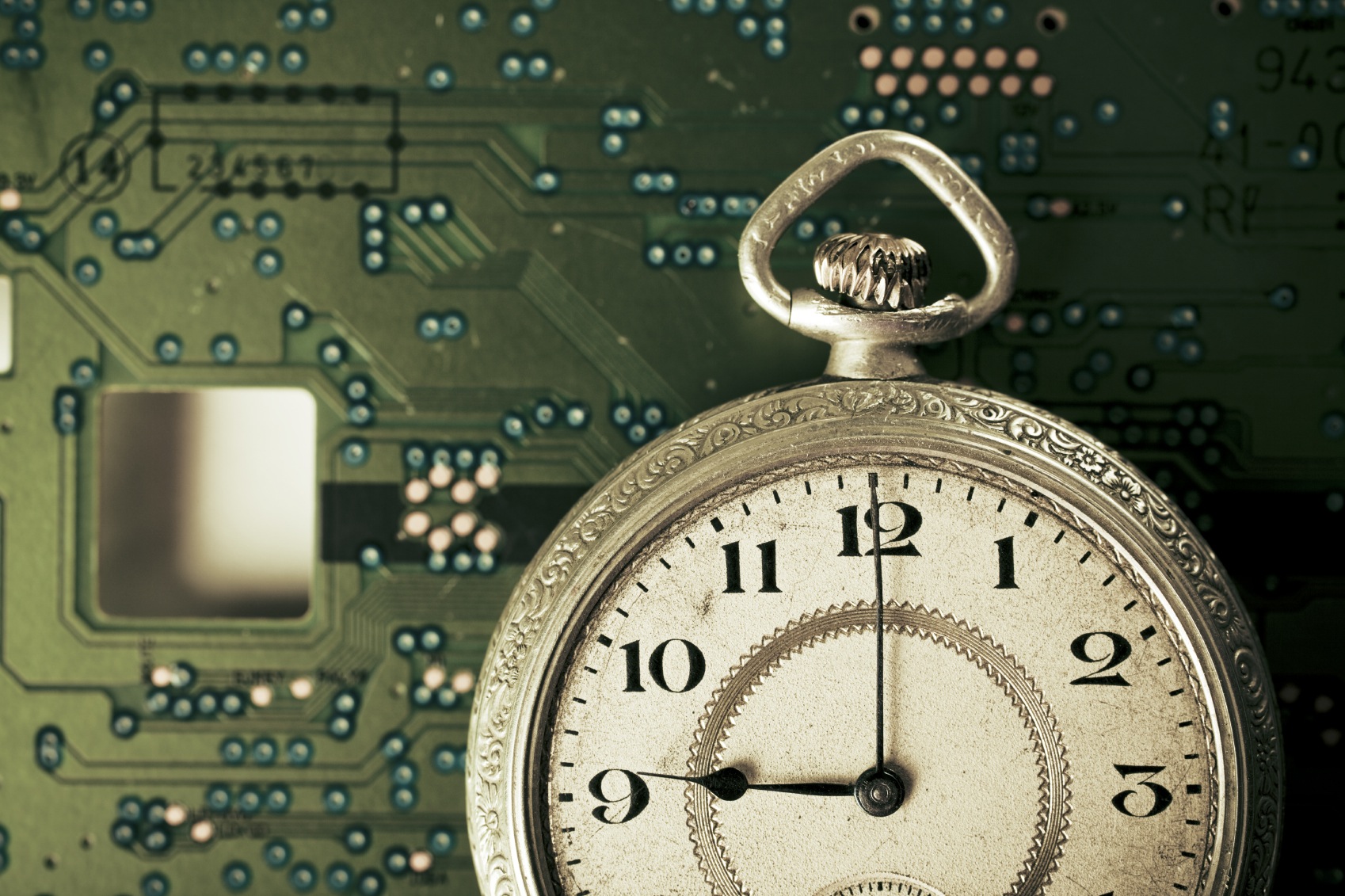
An Electronic component becomes obsolete when it is no longer available from the original manufacturer to the original specification. This is the reason why obsolescence management is now an essential part of the product support activities in sectors such as defense, aerospace, nuclear and railway; where systems need to be supported for several decades.
If your organization Designs, Manufactures, Supplies, Services or uses Systems or Equipment that are designed to provide years of reliable service, the chances are that your organization is at significant risk of the global market forces driving component Obsolescence. To manage the impact on system support, and in turn the costs of ownership, it is vital to be able to capture data that can identify obsolescence cases and resolve them appropriately.
Obsolescence Management must be seen as an integral part of the design, development, procurement, production and in-service Customer support Program – a requirement that involves the complete supply chain.
First, for all long-life, high-reliability, capital investment products, the Project Manager at the beginning of a project should produce an outline Obsolescence Management Plan. This would define who would be responsible for maintaining a product/equipment throughout its project life. If the contractors acknowledge this responsibility, then they should supply a costed Obsolescence
Management Plan embracing the life of the project, and this requirement should be an integral part of the Invitation to Tender (ITT). The plan should be subject to regular review and maintenance
and form part of, or be referred to in the Through Life Management Plan.
A single obsolescence strategy only works if all the products being managed have identical technology needs, operating environments, in-service and support requirements, and the same contractual management demands. Therefore, once a company begins the process of defining an obsolescence strategy, it quickly becomes apparent that there is no simple, formulaic path to risk
assessment. Different products will need different strategies.
A cultural change is required in many business sectors to recognize the significant effects of obsolescence on their continued longer term commercial viability. For designers, manufacturers and suppliers, development of effective obsolescence management processes, as part of both supply chain and new product design management, is essential in order to remain competitive.
In order to manage obsolescence effectively, it is essential to perform an obsolescence risk assessment for the Bill of Materials. The best practice in obsolescence risk assessment, based on a benchmarking study, has been described in this paper.
The key factors that have to be analyzed in the obsolescence risk assessment process for each component in the Bill of Materials are: number of manufacturers, years to end of life, stock available, consumption rate and operational impact criticality.
For the very high risk components, a more detailed analysis is required to inform the decisions regarding the most suitable mitigation strategies.